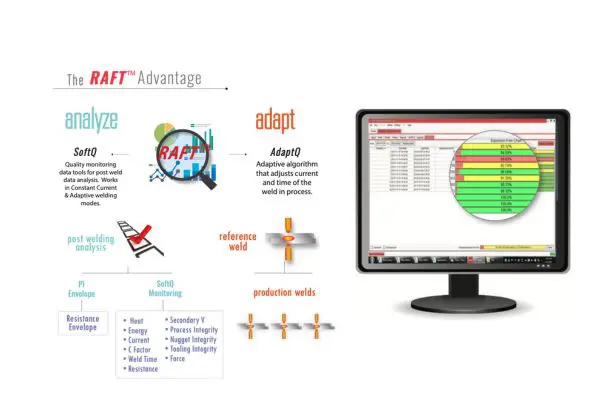
RAFT™
Take control of your resistance welding process with the implementation of RAFT™ (Resistive Adaptive Feedback Technology) software.
- RAFT™ eliminates the hassle and wasted time associated with manually adjusting weld times due to interruptions faced in manufacturing facilities.
- RAFT™ provides support in the resistance welding fabrication process by automatically adjusting your constant current program through adaptive changes in current and/or time as needed to overcome welding disturbances.
- RAFT™ will maintain consistency in your welding process and indicate when secondary tools need maintenance.
Key benefits with RAFT™
RAFT™ will adapt the welding program by current and/or time to address welding disturbances, such as:
- Adjustment of parts
- Variations in part thickness
- Misaligned electrodes
- Variations in coatings
- Sealants
- Variations in welding force
- Deviations
- Machine tool degradation
RAFT™ option for the WT6000
The WT6000 offers a new inverter technology platform designed for rapid data collection, transmission and data analysis. The programming style is consistent with previous series controls from Welding Technology Corp. The ease of programming is well suited to the intuitive style of RAFT™ programming.
Setting up RAFT™ is easy
- Create your constant welding schedule.
- Activates the reference mode.
- Welding.
- Verify that the spot weld is acceptable in size and strength.
- Establishes as reference.
- Activates the AdaptQ TM mode.
RAFT™ consists of two independent software components.
- RAFT™ = AdaptQ™and SoftQ™.
AdaptQ™ is a software algorithm designed to manipulate both current and time according to the resistive feedback of the weld taking place. You decide how much current and time your process can safely allow for maximum productivity.
SoftQ™ can accurately measure the resistance of welding electrodes after they have been sharpened. Although sharpeners can remove edge dross, the control can identify whether the electrode surface has been returned to an approved condition. The SoftQ™ graphing tool analyzes the results of the tip sharpening operation, allowing you to set a warning level and a failure level.