5 Señales de alarma en el manejo de un robot para evitar accidentes
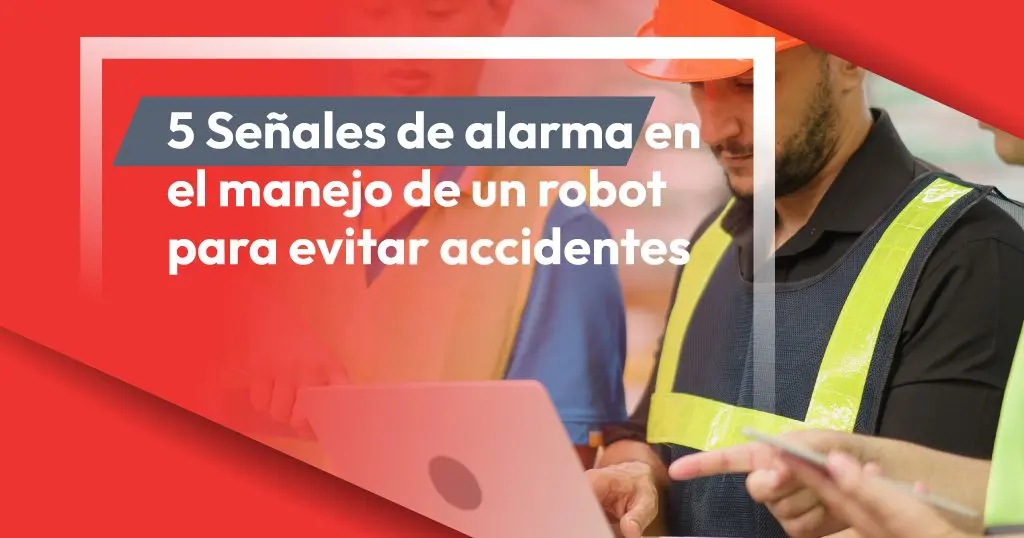
Como sabemos la importancia y el papel de la automatización es cada vez mayor en todas las industrias que utilizan procesos de Soldadura; y aunque esto en realidad ya es muy común, el uso de robots es un tema lleno de importantes detalles y pormenores a considerar, y, justamente, uno de estos elementos será el de la seguridad. Así que, para profundizar más en esto, hoy le mostraremos las 5 señales de alarma en el manejo de un robot, para que así, usted esté preparado ante cualquier eventualidad.
1. No hay un buen sistema de seguridad
La primera de las señales de alarma en el manejo de un robot se trata de uno de los elementos más indispensables en cualquier planta industrial, es decir, contar con un buen sistema de seguridad que incluya:
- Equipo completo para soldadores, incluyendo: máscaras, guantes, zapatos de seguridad, equipo de protección de vista, etc.
- Instauración de procedimientos y medidas de uso de la maquinaria.
- Falta de capacitación y exceso de rotación de personal.
- Uso de distancias y perímetros de seguridad.
- Mal estado o instalaciones inadecuadas (incorrecta circulación de personas, flujo inadecuado de producción, ensamblaje de máquinas y tecnologías de distintas procedencias).
Lo anterior, asegurará no solamente el buen funcionamiento del robot y herramentales anexos, sino que también, reducirá al máximo los posibles accidentes laborales.
2. Falta de conocimiento en el manejo y funcionamiento de los robots
Retomando uno de los puntos anteriores, otra de las señales de alarma en el manejo de un robot se trata de la falta de capacitación en el manejo y funcionamiento de los mismos, pues, aunque suelen tener dispositivos de control relativamente sencillos de usar, éstos tienen una línea de trabajo muy distinta en relación a máquinas convencionales, incluyendo:
- Movimiento simultáneo o independiente de sus ejes.
- Selección y programación de trayectorias complejas y no lineales.
- Campo de acción fuera del área o volumen cubierto por el robot, es decir puede haber espacios de trabajo no reconocidos.
- Campo de acción solapada con otras máquinas y dispositivos.
Elementos que pueden causar diferentes accidentes como colisiones entre robots o contra operadores, aplastamientos, y proyecciones de piezas o materiales; los cuales pueden agravarse por la alta velocidad, energía y dinámica con la que trabajan.
3. Falta de limpieza y mantenimiento de los robots
Por otro lado, una más de las señales de alarma en el manejo de un robot radica en detectar que existe falta de limpieza y/o mantenimiento, pues al carecer de ellos (ya sea completa o parcialmente), pueden presentar:
- Malos funcionamientos en los sistemas de control e interfaces.
- Rotura o desgaste de partes o máquinas, ya sea por uso o corrosión en actuadores, manipuladores, articulaciones, elementos neumáticos y eléctricos y dispositivos de entrada y salida.
- Descomposturas en equipo periférico, tales como bandas transportadoras, elevadores, procesadores especiales y herramental extra de fijación y soporte.
- Falta de liberación de energía residual.
- Sobrecargas por manejos, cargas o tiempos excesivos de operación.
- Acumulación de residuos y contaminantes.
Así como la falta de detección en necesidades de cambios de herramentales u otros aditamentos como son los dress packs para robots.
Recuerde que, aproximadamente, el 90% de los accidentes en líneas robotizadas ocurren durante las operaciones de mantenimiento, ajuste o programación, mientras que sólo el 10% ocurre durante su funcionamiento normal.
4. Los robots no tienen buenos dispositivos de protección
La cuarta de las señales de alarma en el manejo de un robot se trata de la carencia de buenos dispositivos de protección y seguridad inherentes al robot, como pueden ser:
- Sensores: Los cuales deben ser de 2 tipos: internos (de velocidad y de fuerza) y externos (de contacto y no contacto).
- Sistemas de refrigeración.
- Válvulas y watersavers de control de agua.
- Puertas de acceso y barreras.
- Interruptores.
- Sistemas de bloqueo y control.
- Detectores de sobreesfuerzo.
- Frenos mecánicos adicionales.
- Dispositivos de intercambio de piezas.
Los cuales, además, deben de cumplir con el Estándar Nacional Americano para Robots Industriales y Sistemas de Robots, a fin de garantizar el funcionamiento del sistema robótico bajo los mejores parámetros.
5. Otras señales de alarma
Finalmente, otras señales de alarma en el manejo de un robot pueden ser de naturaleza muy variada, por lo cual, le presentamos al menos 5 puntos más que le recomendamos que considere:
- Cuidado con el cableado: Pues se deben revisar flexiones, daños, desgastes y cortes en los cables; además de realizar canalizaciones correctas entre las partes, controladores, y equipos.
- Falta de determinación de límites del sistema: Pues deben delimitarse espacios, tiempos e intenciones de uso.
- Falta de identificación y descripción de peligros y riesgos que pueda generar el trabajo del robot.
- Falta de paradas de emergencia, límites de velocidades máximas y otros sistemas de autodiagnóstico.
- Falta de señalización adecuada y/o mecanismos audibles.
Ya que, lo anterior, junto con una buena normatividad de uso y seguridad, garantizará los resultados de trabajo de la Soldadura automatizada de la forma más confiable y segura.
Señales de alarma en el manejo de un robot
Como sabemos, hay muchos tipos de robots industriales que actualmente están siendo utilizados debido a sus características de multifuncionalidad, control y programación; y no obstante que existen riesgos inherentes a su propio funcionamiento (como, por ejemplo, arranques accidentales), también es cierto, que, prestando atención a las señales de alarma en el manejo de un robot, usted podrá minimizar al máximo los accidentes, descomposturas o paros de producción inesperados.
Recuerde que los costos de reparación de un robot suelen ser bastante elevados, por lo que un programa adecuado de mantenimiento y supervisión de su correcto funcionamiento le ahorrará costos innecesarios, además de maximizar la calidad y eficiencia de su producción.