¿Cuáles son los parámetros de Soldadura que debes regular?
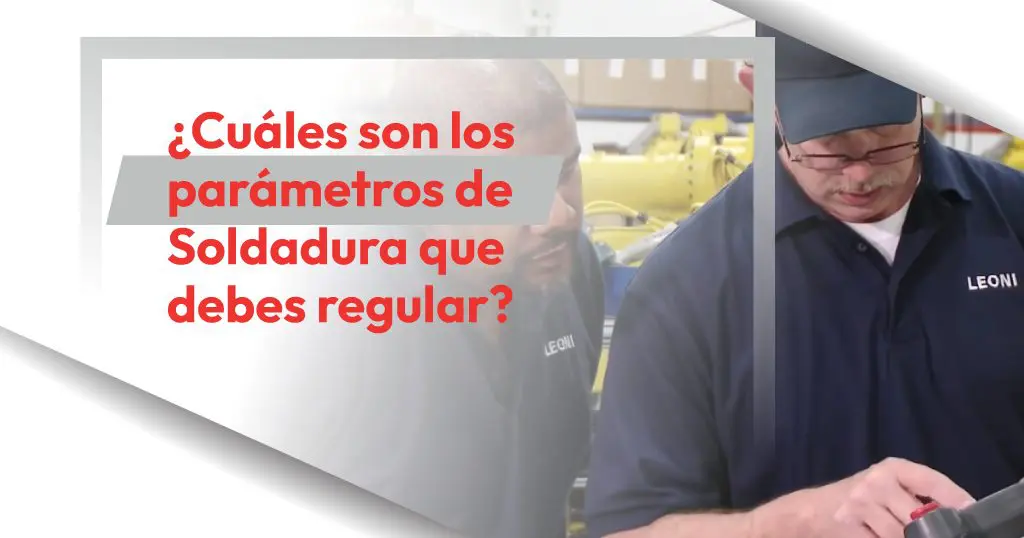
Como ya sabemos, existen ciertos elementos que conforman lo que se puede considerar como un control de calidad para Soldadura, pero además de estos, también existen algunos parámetros de Soldadura básicos que forzosamente se deben de considerar para poder obtener una buena unión en los materiales.
Por lo tanto, el día de hoy haremos un repaso a los mismos, para que así usted pueda recordar junto con nosotros, algunas de las bases y raíces de nuestros procesos de soldeo.
¿Quiere contar con la mejor asesoría en Soldadura? Por favor contáctenos.
1: Electrodos correctos
Desde los más sencillos a los automatizados, los electrodos se vuelven uno de los parámetros de Soldadura más importantes, debido a que la selección de su tipo, diámetro y geometría será esencial para poder llevar a cabo las diferentes tareas de soldeo a realizar.
En este caso, además de seguir las normas de aplicación de la A W.S. y la A.S.M.E., estos siempre se elegirán dependiendo de su tipo de aleación incorporada, su material de aporte, y por supuesto, en función de la composición química y física de los materiales a soldar.
Por otro lado, recuerde que, además, siempre será necesario ponerle atención a su buen estado y correcto almacenamiento, manteniéndolos secos y bien conservados.
2: Intensidad (Amperaje) y tiempo de Soldadura
El segundo de los parámetros de Soldadura es el factor más influyente para poder alcanzar la temperatura y el calentamiento necesarios para la unión final; teniendo una relación directa con el tiempo, pues a mayor intensidad se requerirá menor tiempo de soldeo, y viceversa.
Así mismo, y en relación con la intensidad, la regulación del amperaje en la máquina será también decisiva, pues a cada diámetro de electrodo le corresponde determinados parámetros (mínimos y máximos) de amperaje, mismos que deberán ser regulados hasta un punto de equilibrio que permita el máximo aprovechamiento del electrodo para cada tipo de material, pues de lo contrario pueden suceder 2 problemáticas esenciales:
- Amperaje excesivo: Provoca porosidades, cordones chatos, recalentamiento del electrodo y salpicaduras.
- Amperaje insuficiente: Produce abultamientos y mala penetración en el material, así como dificultades con el arco.
De ahí que se tenga la relación directa con el primero de los parámetros de Soldadura, pues el amperaje correcto dependerá de la selección adecuada del diámetro del electrodo.
3: Resistencia eléctrica de la unión
La resistencia es el parámetro de Soldadura que influye de forma directa en la cantidad de calor generado durante el proceso, teniendo como factores esenciales los siguientes:
- Temperatura: A mayor temperatura menor resistencia.
- Fuerza aplicada a los electrodos: A mayor presión en las piezas a unir, menor la resistencia de contacto.
- Estado superficial de las superficies a unir: A mayor limpieza y eliminación de rugosidades, menor resistencia.
- Estado de conservación de los electrodos: A mayor desgaste y deterioro, mayor aumento en las resistencias de contacto.
Es por esto que, al inicio de la Soldadura la presión debe ser baja, con una resistencia alta y temperatura moderada, mientras que cuando se inicia la fusión, la presión debe de subir para expulsar los gases, reducir la resistencia y provocar el punto de unión; conformándose así la máxima de: a mayor conductividad eléctrica menor resistencia al paso de la corriente.
4: Longitud correcta del arco
El cuarto de los parámetros de Soldadura es muy importante, debido a que su incorrecta medición nos puede llevar a tener importantes defectos en la Soldadura por arco, y ya que no es posible determinarla en mm o pulgadas, esta se deberá medir a través de los resultados de deposición del metal, es decir, por la forma del cordón y el comportamiento del arco.
Cualquier imprecisión en la longitud, puede ser un verdadero problema, pudiéndole generar alguna de las siguientes situaciones:
- Longitudes muy cortas: Cordones con sopladuras, escoria, de poca penetración, gruesos e irregulares; además de interrupción del arco lo cual causa que el electrodo tenga tendencia a pegarse al metal base.
- Longitudes muy largas: Salpicaduras, penetración insuficiente, cordones con sobremontas, porosos y de anchos indeseables.
Por lo que es necesario que la medición se haga lo más exactamente posible.
5: Ángulo correcta del arco
El ángulo correcto del arco es el parámetro de Soldadura que se refiere al apropiado ángulo de inclinación del electrodo, pues este tendrá relación directa con la forma y aspecto del cordón, así como con el nivel de penetración.
De ahí que una mala posición pueda provocarle alguno de los siguientes problemas:
- Ángulo muy cerrado: Mala confirmación del cordón, bajo nivel de penetración, y deposición excesiva del metal de aporte.
- Angulo muy abierto: Cordón irregular con ondulaciones pronunciadas y formación de crestas, expulsión de escoria y bajo recubrimiento.
Por lo que queda claro porque es tan importante el poder trabajar con el ángulo de inclinación correcto.
6: Apropiada velocidad de avance
El último de los parámetros de Soldadura tiene que ver con el equilibrio en la velocidad de avance del electrodo, la cual no debe ser muy lenta o muy excesiva, pues también puede producir los siguientes defectos de Soldadura:
- Velocidad muy rápida: Deficiente fusión del metal con porosidades y cordón delgado, fibroso y con poca penetración.
- Velocidad muy lenta: Abultamiento y desborde del metal de deposición, así como incrustaciones de escoria en la unión soldada.
Por lo tanto, el tener una adecuada velocidad de avance nos producirá uniones limpias y libres de óxido, aceite y grasa.
Parámetros de soldadura
Como pudo ver, si usted desea una Soldadura de alta calidad y libre de defectos, hay bastantes parámetros de Soldadura en los cuales fijar su atención; y aunque la mayoría de los estándares de producción se alcanzan a base de prueba y error, también recuerde que los equipos actuales de control de Soldadura están totalmente automatizados, lo cual le ayudará a establecer y controlar sus parámetros de forma independiente y automática.
No obstante, es muy importante recalcar, que es vital que usted y sus operadores conozcan la teoría detrás de cada elemento, pues su comprensión los llevará a tomar mejores medidas preventivas y correctivas.