¿Cómo calcular la eficiencia energética del equipo de Soldadura?
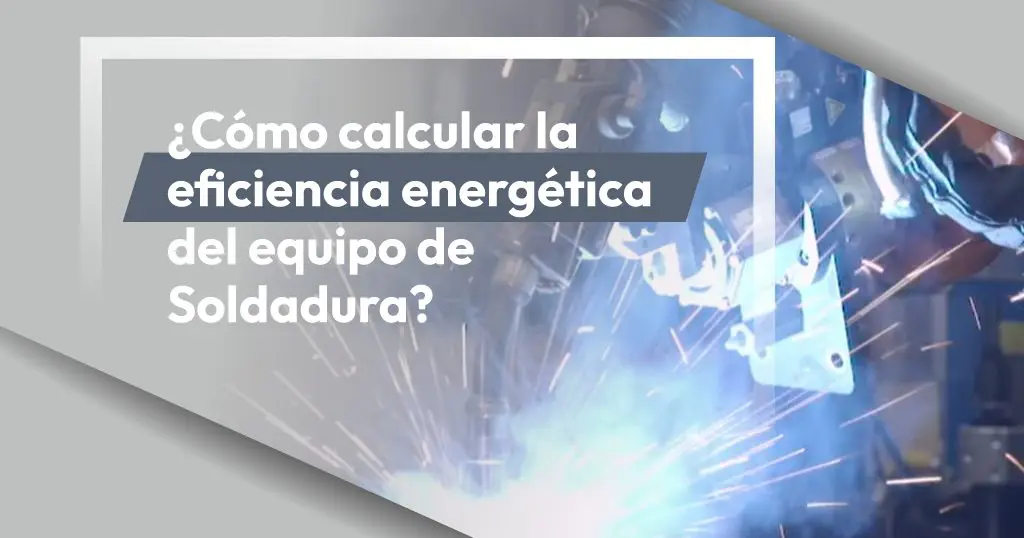
Actualmente, existen muchos retos a los cuales se está enfrentando la industria manufacturera que utiliza procesos de Soldadura por Resistencia. Y, uno de los más importantes en la actualidad, es el tema del ahorro energético; principalmente, debido a las necesidades de ejecutar líneas de producción simultáneas, con grandes capacidades y, claro, alta calidad. Así que, ¿Cómo calcular de forma acertada la eficiencia energética del equipo de Soldadura?
El día de hoy veremos sus pormenores, para que así, usted pueda realizar mediciones correctas y concretas, a fin de que desarrolle planes de evaluación, mantenimiento y corrección en sus equipos.
Paso 1: Evaluación física de equipos de Soldadura
El primer paso para medir adecuadamente la eficiencia energética del equipo de Soldadura es, por supuesto, una meticulosa revisión física, en la cual le recomendamos prestar especial atención a los siguientes puntos:
- Revisar condición de todos los equipos, prestando especial atención a aquellos que tienen más de 4 años de uso, pues es probable que no cuenten con la tecnología de ahorro de otros equipos más actuales.
- Detectar equipo roto y con fallas, recuerde que, aunque sigan operando, los costos de equipo defectuoso pueden resultar más altos a largo plazo (incluso que renovarlos) debido a sus resultados de baja calidad.
- Revisar y determinar a qué equipos se les puede realizar actualizaciones de software o mejoras herramentales, y cuáles deben sustituirse por completo.
Recuerde que, a pesar de qué este tipo de acciones representarán gastos, el retorno de la inversión será excelente y a muy corto plazo.
Paso 2: Evaluar los materiales
Recordemos que la eficiencia energética del equipo de Soldadura también dependerá de los materiales que se usarán, pues su naturaleza alterará la cantidad de energía requerida:
- Conductivo: Oro, Plata, Cobre, Aluminio
- Medio: Bronce
- Resistente: Molibdeno, Tungsteno, Níquel, Titanio, Berilio
Por lo cual se podrían buscar aleaciones entre los diferentes metales para tener diferentes y mejores niveles de conductividad eléctrica, maleabilidad, dureza y resistencia.
Paso 3: Calcular potencia de entrada de los equipos
Profundizando más en la medición de la eficiencia energética del equipo de Soldadura, pasamos a un punto crucial para saber a ciencia cierta cuánta energía consume cada máquina, para lo cual, habrá que calcular 3 elementos:
- Potencia eléctrica: Voltaje por corriente.
V (voltaje) X I (corriente/intensidad).
- Energía consumida: Potencia demandada por unidad de tiempo.
Q (energía/calor) = W (potencia) X t (tiempo).
- Potencia de entrada: Fuerza que absorben los equipos de las fuentes eléctricas.
WE = WS (potencia de salida) / Eficiencia de la fuente de la corriente (datos que deben ser proporcionados en la información técnica de los fabricantes).
Cálculos que se obtendrán en Watts o Vatios (W) y que le permitirán conocer la potencia y energía requeridas en cada máquina, para así realizar comparativos de eficiencia entre sus equipos y, por supuesto, contra otros más nuevos en el mercado.
Paso 4: Calcular costos de funcionamiento
Otro paso esencial en el cálculo de la eficiencia energética del equipo de Soldadura
será conocer los costos de funcionamiento de estos durante los procesos de Soldadura, mismos que se obtendrán multiplicando la potencia de entrada (ver punto anterior) por el número de horas en que la fuente de corriente se encuentre activa, por el precio del KW por hora.
De esta forma, usted obtendrá el cálculo exacto del costo de funcionamiento de cada uno de sus equipos, pudiendo medir su eficiencia real en cuanto a ahorro de energía.
Considere que la CFE proporciona energía a 60 Hertz (ciclos) y que pueden existir variaciones; y aunque estos pasan por diodos rectificadores, le recomendamos usar equipos como reguladores para proteger los equipos.
Paso 5: Calcular costos de operación durante periodos de inactividad
Así como es importante calcular los costos de consumo durante los periodos de funcionamiento, será igual de importante calcular los costos durante los tiempos de inactividad, para lo cual, habrá que multiplicar la potencia de entrada del punto 2, por las horas o minutos de inactividad al día, por el precio de KW por hora o minuto.
Así, usted podrá saber el costo de tener inactivos sus equipos por día, semana, mes y hasta año, siendo un dato muy importante, pues existen industrias con producciones muy costosas (como la automotriz), que pueden verse seriamente afectadas en utilidad, por incluso, minutos de paro al día.
Paso 6: Calcular el costo total de su operación
Finalmente, para terminar de medir la eficiencia energética del equipo de Soldadura, será necesario sumar los cálculos de los puntos 3, 4 y 5, para que así obtenga el costo total de la operación, a fin de que determine si sus equipos le están brindando:
- La productividad que requiere.
- El retorno de la inversión necesitada.
- La utilidad mínima después de costos.
Lo que le permitirá determinar si los equipos están en óptimas condiciones, si requieren de refurbish o algún herramental extra o si, por el contrario, requieren de un reemplazo completo.
Calcular la eficiencia energética del equipo de Soldadura
Contar con el nivel óptimo de eficiencia energética del equipo de Soldadura es una cuestión que se logra contemplando el proceso de producción de forma integral, contando con una evaluación concienzuda y metódica de los equipos, materiales, energía, tiempo y de todos los demás elementos que pueden alterar el resultado de Soldadura.
Por supuesto, posteriormente, es muy probable que se deberán hacer cambios, pero estos pueden darse de forma paulatina, de acuerdo a las necesidades y posibilidades de cada empresa; pudiendo comenzar con la instauración de nuevas políticas de trabajo y ahorro, compra de herramentales o aditamentos extras y, en una etapa posterior, la adquisición de equipos más actuales y automatizados.