Los 6 mejores ensayos no destructivos usados en Soldadura
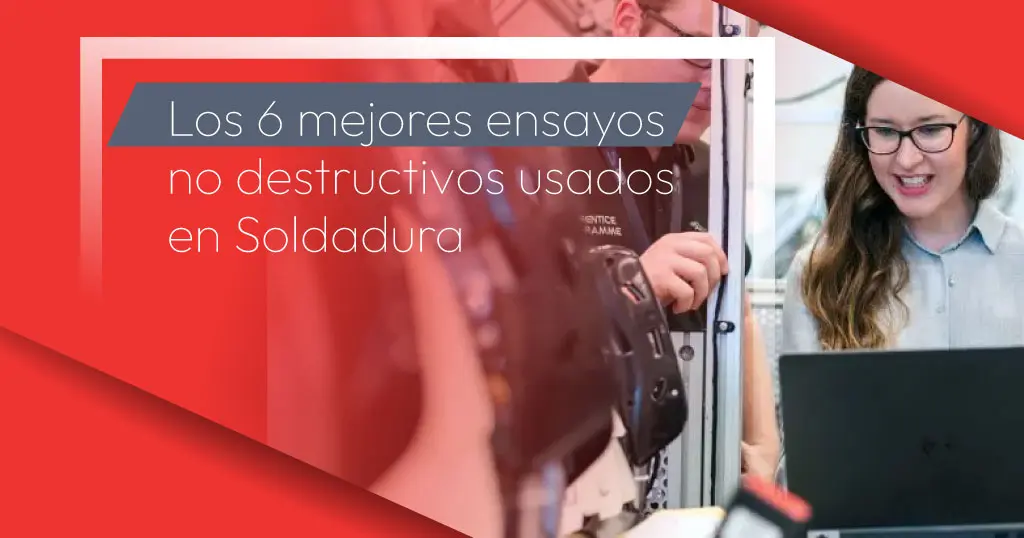
Como comentamos, la calidad en la Soldadura por resistencia es algo que debemos cuidar por todos medios, así que, a diferencia de las pruebas destructivas que vimos en la entrada anterior, hoy revisaremos los 6 mejores ensayos no destructivos usados en nuestra industria.
Así que, por favor, siga leyendo y conózcalos.
¿Qué son los ensayos no destructivos en la Soldadura?
En este caso, los ensayos no destructivos son técnicas no invasivas para determinar la integridad de un material, componente, unión o estructura o para medir cuantitativamente sus características, además de que:
- No afectan a las propiedades físicas, dimensionales, químicas o de uso de las piezas muestreadas.
- Permiten la detección de grietas, porosidades, penetraciones incompletas, inclusiones, discontinuidades (superficiales e internas), defectos y deformidades que pudieran comprometer la resistencia de la Soldadura.
- Se pueden inspeccionar diversos materiales, incluyendo metálicos y no-metálicos.
Así mismo, este tipo de pruebas suelen ser más baratas pues no implican la destrucción de la pieza, aunque suelen ser menos cuantificables pues se basan en verificar la homogeneidad y continuidad del material.
1: Inspección visual de Soldadura
Pues, iniciamos con el que es, hasta cierto punto, el más obvio de los ensayos no destructivos, pues se trata de la observación de toda la secuencia de operaciones a lo largo del proceso productivo, teniendo como objetivo la calidad de las uniones soldadas y teniendo que tomar en cuenta que:
- Al finalizar, se debe llevar un reporte de inspección, en el cual se identifican materiales que incumplen especificaciones o las zonas a reparar.
- Aunque es visual, se pueden usar algunos instrumentos como cintas métricas, reglas, escuadras, calibradores, equipos de medición de temperatura o presión, dispositivos de iluminación y medios ópticos auxiliares.
Además de que reduce la necesidad de ensayos no destructivos posteriores, al mismo tiempo que facilita la corrección de defectos de forma sencilla y rápida; aunque eso sí, su fiabilidad puede llegar a ser muy dependiente de la habilidad y la experiencia del operario o supervisor.
2: Ensayos con líquidos penetrantes
El segundo de los mejores ensayos no destructivos consiste, literalmente, en la aplicación de un líquido sobre la superficie del cuerpo a examinar, que penetra por capilaridad en las imperfecciones de la Soldadura; teniendo, además, las siguientes características:
- Se hace mediante la aplicación de un líquido con buenas características de penetración para, después, aplicar un líquido absorbente (revelador) de diferente color, el cual absorberá el líquido que haya penetrado, revelando las aberturas, imperfecciones, poros, fisuras, etc.
- Existen 2 tipos de líquidos penetrantes:
1.- Fluorescentes: Contienen un colorante que se ilumina bajo la luz negra o ultravioleta.
2.- No fluorescentes: Contienen un colorante de alto contraste bajo luz blanca.
- De esta forma, las imperfecciones aparecen marcadas de forma clara y exacta a lo largo de la pieza a examinar.
Siendo muy simple de aplicar y de interpretar, aportándonos un excelente nivel de precisión.
3: Ensayos con partículas magnéticas
Este tercer tipo de ensayos no destructivos se basa, por supuesto, en el magnetismo de materiales ferrosos como el acero, pues si estos presentan alguna discontinuidad superficial y/o sub-superficial, ésta actuará formando polos magnéticos, atrayendo cualquier material magnético o ferromagnético que esté cercano a la misma.
Así mismo, en este tipo de ensayos, habrá que considerar 3 elementos:
- La prueba consta de 3 fases: Magnetización de la zona, repartición de las partículas magnéticas y observación de las indicaciones para detectar las discontinuidades.
- Magnetización de las piezas se puede realizar de 2 formas: Por imanes o por corriente eléctrica.
- Aplicación de las partículas magnéticas puede aplicarse por vía seca (en forma de polvo) o por vía húmeda (con medios acuosos o por disolventes sintéticos).
Siendo un método simple, fácil, portátil y rápido en, prácticamente, cualquier superficie metálica.
4: Ensayo de Ultrasonido
El cuarto de los mejores ensayos no destructivos se basa en la propagación de ondas sonoras a través del material, mediante:
- Un sensor que convierte los pulsos eléctricos en pequeños movimientos o vibraciones, cuyo camino, cuando es interrumpido o tiene un cambio, es detectado y registrado a través de un monitor.
- Detector de fallas portátiles y un palpador angular.
- Un equipo capaz de generar, emitir y captar haces de ondas muy bien definidas, mediante un haz sónico de alta frecuencia (125 KHz a 20 MHz) el cual es circulado en el material a ser inspeccionado.
Detectando las discontinuidades internas y superficiales (fisuras, inclusiones, etc.) con una alta precisión, sensibilidad, transportabilidad y facilidad de operación con resultados inmediatos. Aunque, eso sí, hay que considerar que se requieren operadores y supervisores bastante entrenados.
5: Ensayo por radiografía (rayos X)
El siguiente ensayo no destructivo, consiste en la absorción diferenciada de radiación penetrante por la pieza que está siendo inspeccionada, tomando en cuenta los siguientes elementos:
- La variación en la cantidad de radiación absorbida nos indicará la existencia de una falla interna o defecto en el material.
- La radiografía industrial será entonces usada para detectar variaciones de una región que presenta una diferencia en espesor o densidad comparada con una región vecina.
- Estos defectos como grietas, bolsas, inclusiones, etc. de distintas densidades absorberán las radiaciones en distinta proporción que el material base, de forma que se generan detalles de contraste claro-oscuro en la placa fotográfica colocada detrás de la pieza.
Permitiendo identificarlas sin tener que desarmar las piezas, aunque es importante considerar que se requiere de equipamiento especial, personal entrenado y equipos de tratamiento de imágenes.
6: Pruebas con rayos gamma
Finalmente, el último de los ensayos no destructivos se basa en los rayos gamma, los cuales se producen por transiciones de energía en el interior de núcleos de átomos radiactivos, así como en indicadores de calidad de imagen que consisten en alambres o plaquetas escalonadas del mismo material que el objeto a radiografiar, cuyos diámetros o espesores oscilan del 1 al 3% de espesor máximo del objeto, permitiendo evaluar por comparación la calidad radiográfica.
Detectando así. laminaciones, roturas del núcleo en materiales compuestos y huecos mediante una lectura directa y desde la superficie; aunque, es necesario decir que incluye peligro de radiación y una posible pérdida de sensibilidad dependiendo del espesor del material.
Los ensayos no destructivos
Los procesos de Soldadura por resistencia tienen muchas ventajas, pero no hay que olvidar que siempre deben estar sometidos a controles de calidad continuos que se deben hacer en cada una de sus etapas.
Por lo tanto, los ensayos no destructivos serán una excelente forma de garantizar los resultados y con ellos, la eficiencia de las uniones y piezas terminadas.