5 Mitos sobre la Soldadura por Resistencia
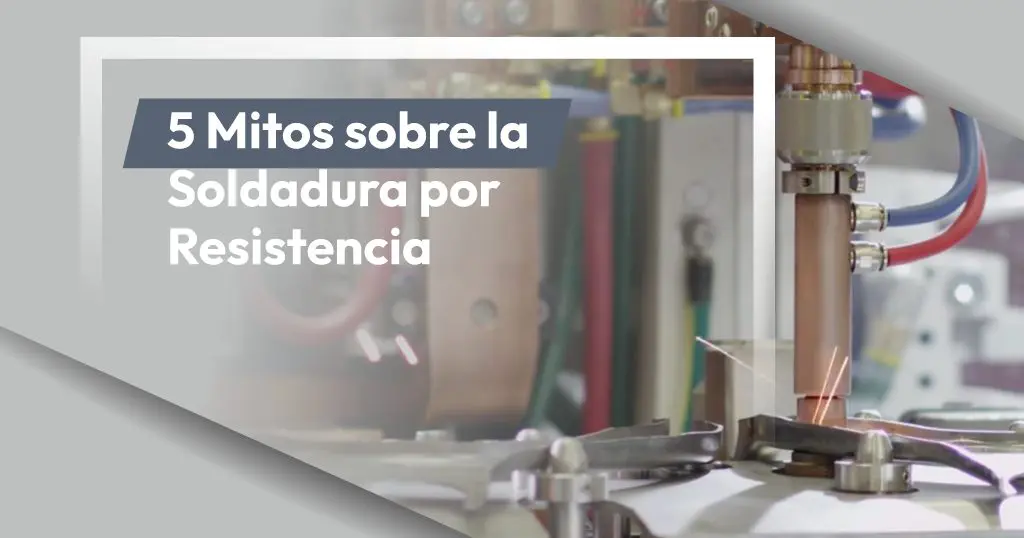
No hay duda de que hoy en día, la eficientización y la mejora de la calidad de la Soldadura por resistencia debe de ir de la mano de la automatización industrial, y con ella, de los sistemas robóticos. No obstante, la conjunción de estos nuevos dispositivos, herramientas, máquinas y formas de hacer las cosas, han hecho surgir nuevos mitos sobre la Soldadura por resistencia, mismos que trataremos de resolver a continuación para esclarecer cualquier duda.
Así que, por favor, siga leyendo a fin de que deje de tomar en cuenta estas falsas afirmaciones y se pueda enfocar en lo verdaderamente importante: mejorar la productividad de sus procesos.
Mito 1: El mantenimiento preventivo no tiene mucho caso
El primero de los mitos sobre la Soldadura por resistencia es aquel que tiene que ver con la idea de que el mantenimiento preventivo no es tan esencial, o al menos que no reditúa tanto como para considerarlo una actividad o un gasto permanente.
Ya que, por el contrario, éste es esencial y mucho más si se utilizan sistemas robóticos, pues será una de las formas más importantes de maximizar el retorno de su inversión.
Por lo tanto, asegúrese de:
- Verificar todas las conexiones del sistema, incluyendo consumibles, pistolas de Soldadura y alimentación eléctrica.
- Revisar si hay desgaste en partes y consumibles, así como salpicaduras.
- Realizar un calendario de mantenimiento para todo el herramental y las partes robóticas.
Recuerde que todo esto puede planearse para realizarse entre las pausas de los ciclos de Soldadura o de los turnos de trabajo. Y que siempre le ayudarán a evitar tiempos improductivos, reparaciones costosas y piezas con baja calidad.
Mito 2: Los consumibles no son tan importantes como las máquinas y las herramientas
El segundo de los mitos sobre la Soldadura por resistencia se basa en creer que basta con mantener el buen estado de las máquinas y las herramientas para obtener una Soldadura de calidad. Ya que por el contrario también es imprescindible que los consumibles con los que trabajemos no presenten daños, pues éstos pueden producir:
- Disminución en la calidad y precisión de las piezas.
- Aumento de tiempos de Soldadura.
- Aumento de bordes biselados.
- Acumulación de escoria.
- Distorsión de bordes en las piezas.
- Deformaciones y defectos en la Soldadura, tales como mal aspecto, salpicaduras, penetración excesiva, agrietamientos, combaduras, deformaciones y socavados.
Por lo que habrá que aprender qué buscar y qué revisar en cada uno de los elementos, además de:
- Calcular el número de piezas y costos por consumible, preferiblemente con un planeación específica para preservar stock.
- Valorar si es necesario cambiar todo el set de consumibles o si se necesita reemplazar algún componente en específico.
Además de nunca olvidar poner atención a todos los consumibles, incluyendo cables eléctricos, portaelectrodos, tuercas, pernos, tapas, anillos, alambres, varillas y puentes laminados.
Mito 3: El buen funcionamiento del electrodo sólo depende de su manufactura
Uno más de los mitos sobre la Soldadura por resistencia se basa en el que es considerado el consumible más importante: el electrodo. Pues si bien, en gran parte, su buen funcionamiento radica en la calidad de su manufactura, también hay otros elementos adicionales que impactarán directamente en su funcionamiento, tales como:
- Intercambiadores de electrodos: Usados para eliminar los tiempos muertos o de paro por el cambio de electrodos en las líneas de producción; reduciendo el trabajo y el control operativo, y con ello, la repetición de errores humanos y el desgaste inútil de las piezas.
- Electrodos inteligentes: Los cuales contienen una visión, a través de fibra óptica, que trasmite la posición del perno guía (con una exactitud milimétrica) a un módulo remoto que compara los valores de medición de cada tuerca.
- Sistemas de almacenamiento y mantenimiento de electrodos y caps.
Dándoles no sólo mayor rendimiento y vida útil, sino también eficientando toda la cadena productiva.
Mito 4: Usar un afilador de electrodos no es tan importante
El cuarto de los mitos sobre la Soldadura por resistencia se trata de la creencia de que el uso de un afilador de electrodos no es tan importante y esto es una idea que es completamente falsa. Pues estos repercutirán directamente en la posibilidad de alcanzar niveles satisfactorios de conductividad eléctrica, resistencia y consumo de energía, a través de:
- Revestir automáticamente las puntas de los electrodos.
- Asegurar la consistencia en el área de contacto de los electrodos.
- Mantener la densidad de la corriente eléctrica de forma constante y precisa.
- Reducir errores manuales, así como tiempos de trabajo y controles operativos.
Logrando un desempeño ideal en cualquier programa de Soldadura, al mismo tiempo que se minimizan las interrupciones del sistema productivo. Mismas que por necesidades no programadas de intercambio de consumibles o por posibles problemas y defectos en las piezas terminadas.
Mito 5: Cuando hay una colisión, lo mejor para recuperar el TCP es reprogramar al sistema robótico
Una colisión durante la Soldadura puede causar la pérdida del llamado “Punto Central de la Herramienta Robot” (TCP), el cual a grandes rasgos es el punto utilizado para el posicionamiento de robots en cualquier programa que implique objetivos definidos en un espacio cartesiano.
Y dada su importancia (ya que la pérdida de este punto implicaría que la programación estuviera fuera de línea) es muy común que se opte por reprogramar el sistema robótico completo, lo cual puede ocasionar que el cuello de la Pistola ya no funcione para ese diseño robótico en específico.
- Corregir la posición del cuello de la Pistola de Soldadura.
- Utilizar aditamentos que verifiquen que la punta de contacto de la Pistola esté en el TCP correcto.
- Adicionar sensores de proximidad que eviten nuevas colisiones.
Eliminando con esto la posibilidad de obtener Soldaduras fallidas o desalineadas, así como problemas de separación de herramental y de sujeciones, así como sus consiguientes costos.
Por lo tanto, y en lugar de realizar directamente esta reprogramación, le recomendamos hacer otras acciones que son más efectivas y menos costosas, tales como:
Mito 6: El retrabajo es algo rutinario en la Soldadura
El último de los mitos sobre la Soldadura por resistencia ya sea con o sin sistemas robóticos, es la falsa idea de que el retrabajo es algo rutinario durante este tipo de procesos, pues como vimos, hay muchas formas de que esto se reduzca al mínimo e, incluso, se elimine.
Por lo tanto, y además de las recomendaciones dadas en los puntos anteriores, también le sugerimos que tome en cuenta las siguientes consideraciones para eliminar de tajo esta concepción:
- Asegúrese no sólo de contar con el equipo y las herramientas correctas, sino también, con el personal capacitado para programar y ajustar los sistemas.
- Tenga proveedores específicos y experimentados en sus diferentes insumos, consumibles, equipo y herramientas que utiliza, y de preferencia tenga un distribuidor o integrador de servicios de Soldadura.
- Integre Controles de Soldadura que le permitan medir, monitorear, detectar y supervisar variables, parámetros y en sí, la calidad completa del proceso de Soldadura.
Así mismo, no se olvide trabajar en todo momento con los elementos de seguridad necesarios, tales como interruptores, sistemas de bloqueo y control, sensores y barreras para mejorar aún más las condiciones de trabajo y, así, eliminar cualquier posible error o accidente.
Termine con los mitos sobre la Soldadura por resistencia
Como vimos, gran parte de la labor de terminar con los mitos sobre la Soldadura por resistencia se trata de mejorar prácticas en temas de programación y selección de herramientas y consumibles, así como de crear una planeación de mantenimiento que permita tener el sistema productivo funcionando de forma óptima, todo el tiempo
Así que, si usted quiere reducir costos, mejorar la calidad y la productividad de sus procesos y bajar (e incluso eliminar) sus tiempos de paro, ponga en práctica algunas de estas recomendaciones. Verá que la inversión le traerá grandes beneficios a corto, mediano y largo plazo.